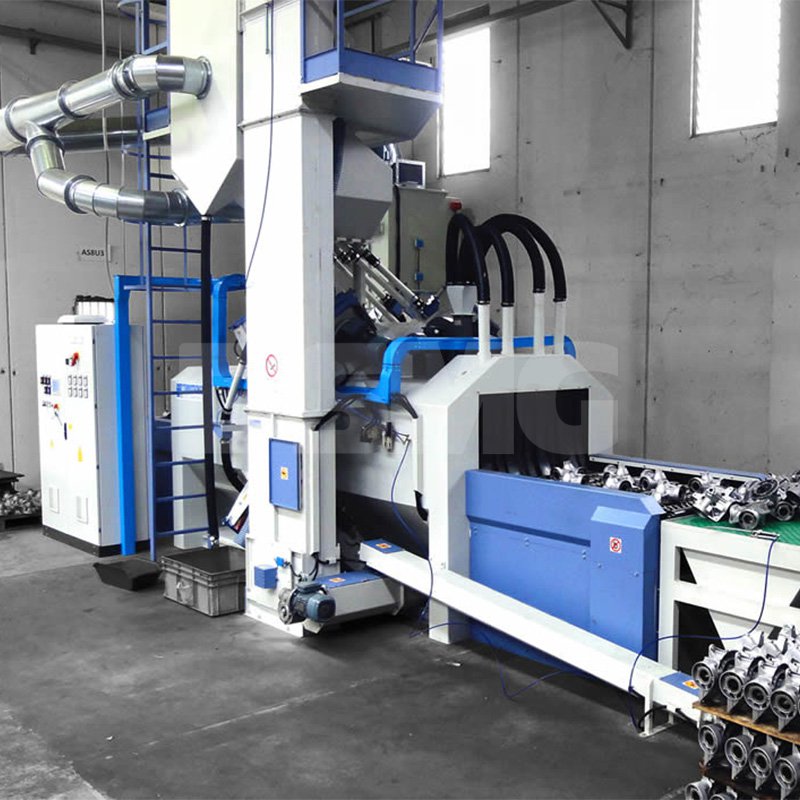
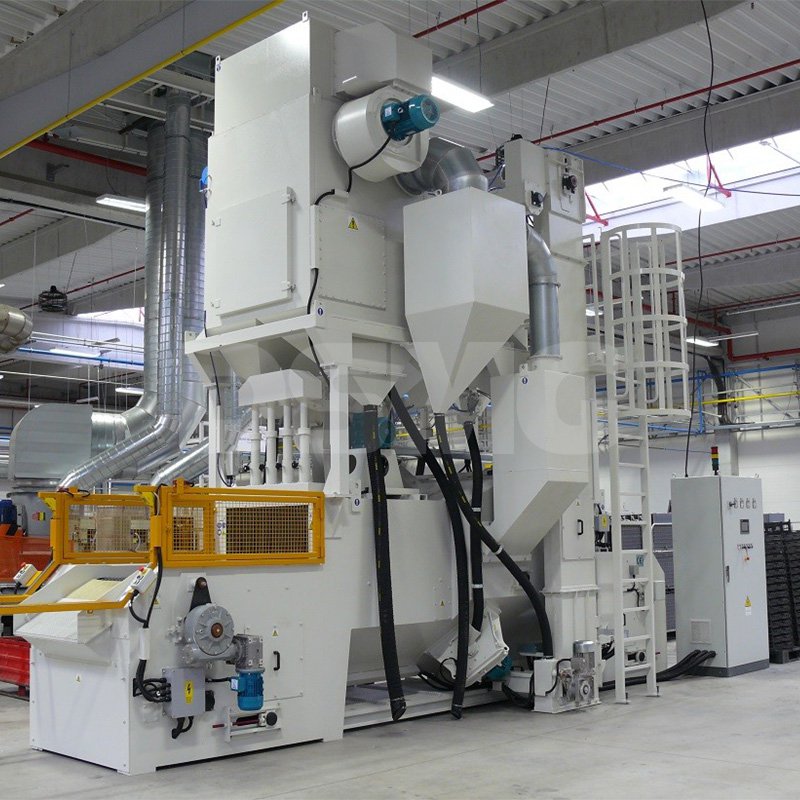
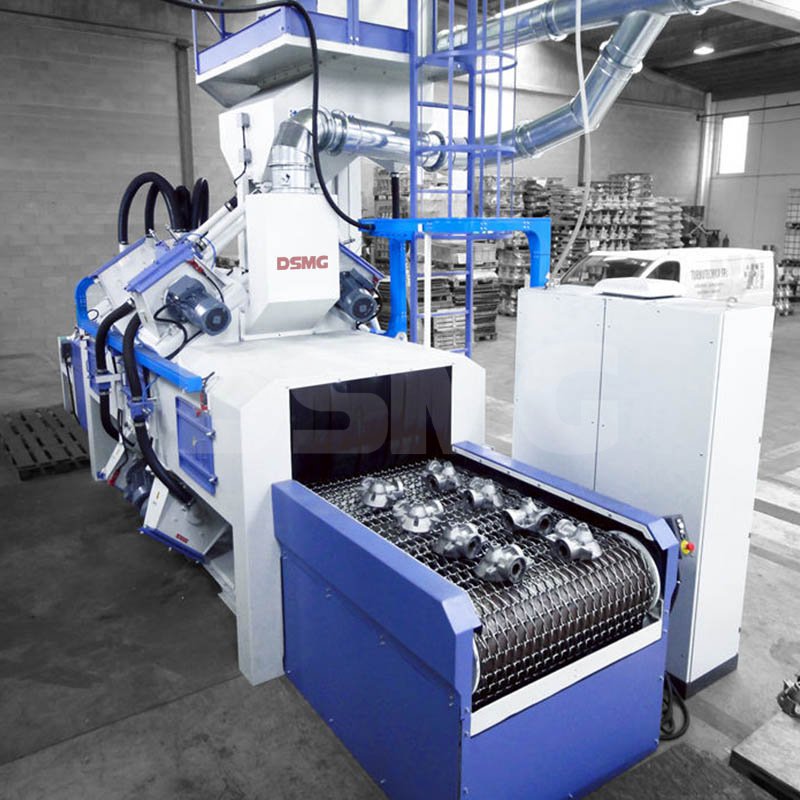
Nemak, a global provider of innovative lightweight solutions for the automotive industry, specializes in developing and manufacturing aluminum components for powertrain and structural body applications. Its primary products include aluminum engine cylinder heads, cylinder blocks, and suspension system components.
Since 2013, DISA has delivered 5 wire mesh shot blasting machines to Nemak. DISA’s direct-drive blast wheels ensure stable production and exceptional performance. The cleaned and recycled abrasive media reduce waste and lower operational costs, solidifying DISA’s position as Nemak’s trusted partner for over a decade.
DISA wire mesh Continuous Shot Blasting Machine efficiently processes diverse parts and castings. Its open-mesh belt design minimizes material handling complexity:
Components are placed on the wire mesh conveyor, which continuously feeds them into the blast chamber through a sealed entrance.
After blasting, parts exit via a multi-stage seal system at the outlet.
Key features:
No pit requirement: Blast chamber lined with manganese steel and replaceable cast liners.
Heavy-duty manganese steel conveyor belt (width: 18"-60", European import), adjustable speed.
8 direct-drive blast wheels (15 kW motors each).
Large-diameter drive rollers reduce belt fatigue; automatic belt tensioning.
Abrasive auto-feeder with overflow hopper for abrasive recovery.
Rotary screener and magnetic separator integrated.
PLC control, touchscreen HMI, and robotic loading/unloading system.
Blast Wheel Mechanism (Core of DISA Machines):
Abrasive flow is optimized via automatically controlled valves to the wheel’s central impeller.
The impeller distributes abrasive evenly through a control cage.
Precise cage adjustment ensures abrasives contact blades at the optimal moment, projecting a focused stream onto workpieces.
DISA’s blast wheel combines proven design with easy maintenance.