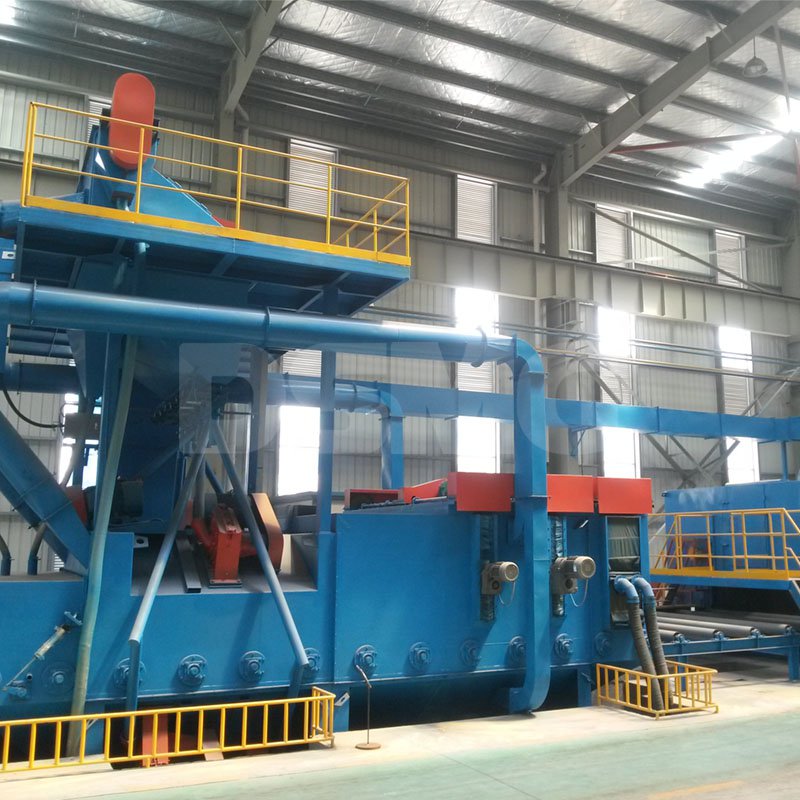
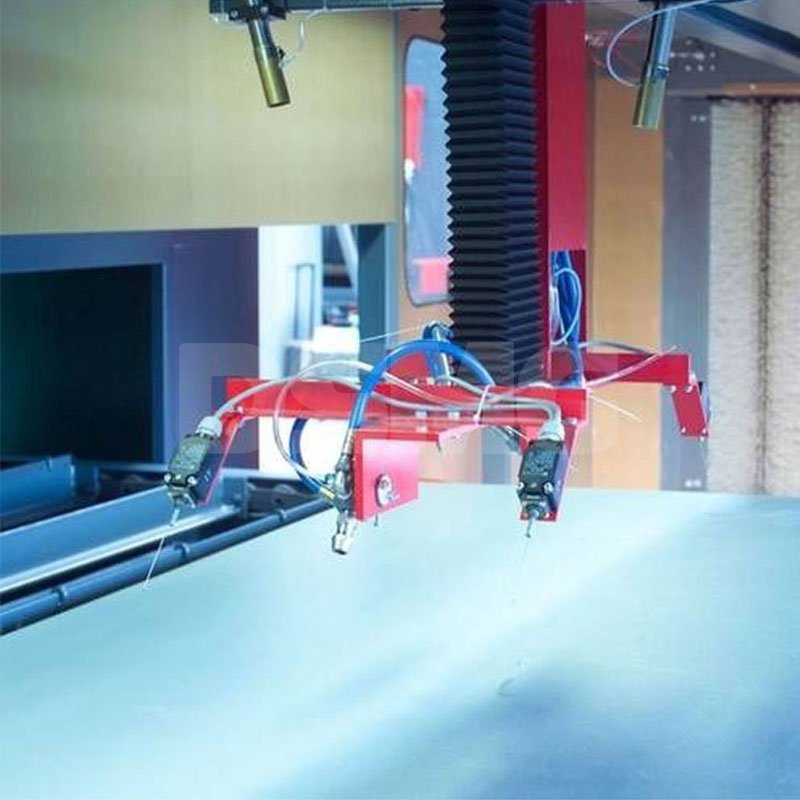

Ningbo NSS Group, as a steel structure manufacturing supplier in fields including power plants, mining, industrial facilities, and amusement equipment, is composed of professional management and technical teams from the United States, China, Canada, Australia, and the United Kingdom.
NSS Group adopts the shot blasting and spray coating systems from Disa's anti-corrosion production line. This shot blasting system is used for rust removal and surface roughening of steel plates and structural profiles. The steel is first dried and preheated, then automatically undergoes shot blasting and spray coating, and is finally dried in a hot air tunnel. This anti-corrosion production line enables NSS Group to clean and coat stock materials according to customer requirements while delivering finished steel products to clients in minimal time.
The Disa steel plate pretreatment shot blasting line is designed to process steel plates up to 4 meters wide, 5 cm thick, and 18 meters long, as well as 1-meter I-beams, with a typical processing speed of 1.5-3 meters/minute. The steel is conveyed into the Disa shot blasting system via roller conveyors. It first passes through a workstation with direct flame preheating to remove surface moisture. The steel then continues along the conveyor into the shot blasting machine, where it is impacted by 12 Disa direct-drive blast wheels, ensuring uniform coverage across the full width of plates and the circumferential surfaces of structural profiles.
After shot blasting, the steel enters the automatic spray booth—a dual-filtration system applies water-based topcoats via HVLP spray guns or solvent-based primers via airless spray guns. The coating system is equipped with real-time monitoring sensors to ensure consistent coating quality while optimizing paint utilization.
Pre-shot blasting reduces wear on cutting tools such as band saws and drill bits, lowering overall production costs. After coating, the steel exits the spray booth into the drying tunnel and is finally discharged from the anti-corrosion line via conveyors.
The spray booth is equipped with a dual-stage filtration system: the first stage uses a reverse-pulse paint filtration unit to remove paint mist particles from the air, and the second stage employs a thermal oxidizer to treat volatile organic compounds. This system prevents harmful paint mist and particles from entering the workshop or external environment, achieving significant waste reduction throughout the process.
With the Disa production line and support from Disa’s services, NSS Group enhances production efficiency through automated shot blasting and spray coating technologies, meeting diverse manufacturing demands.