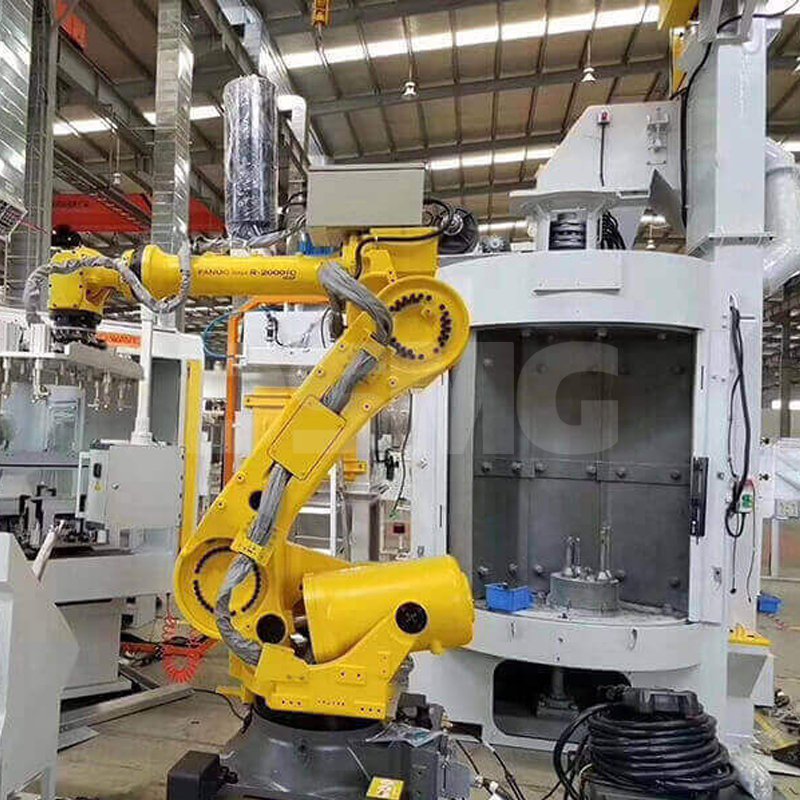
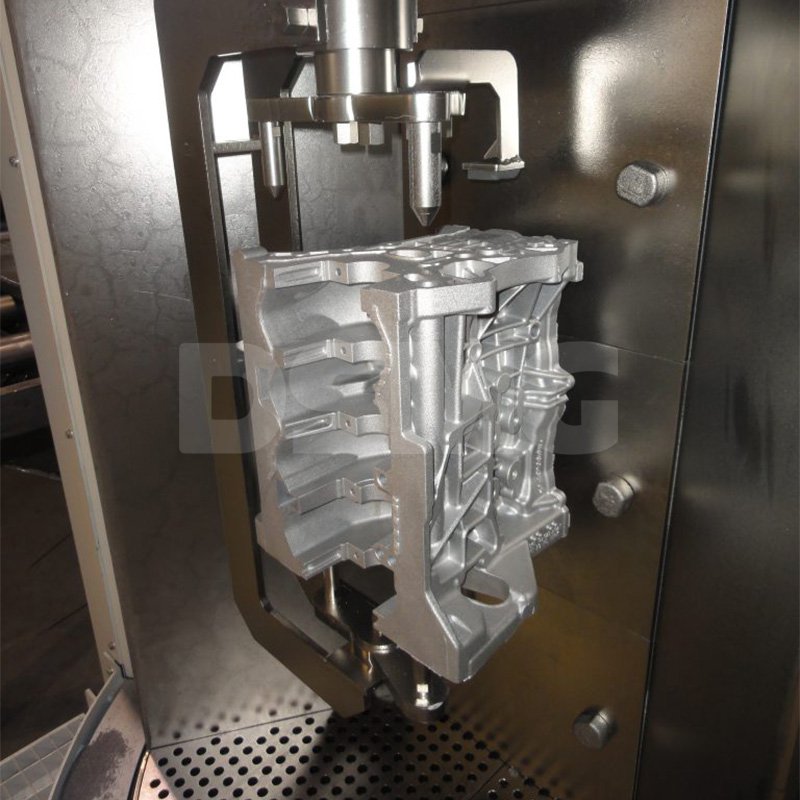
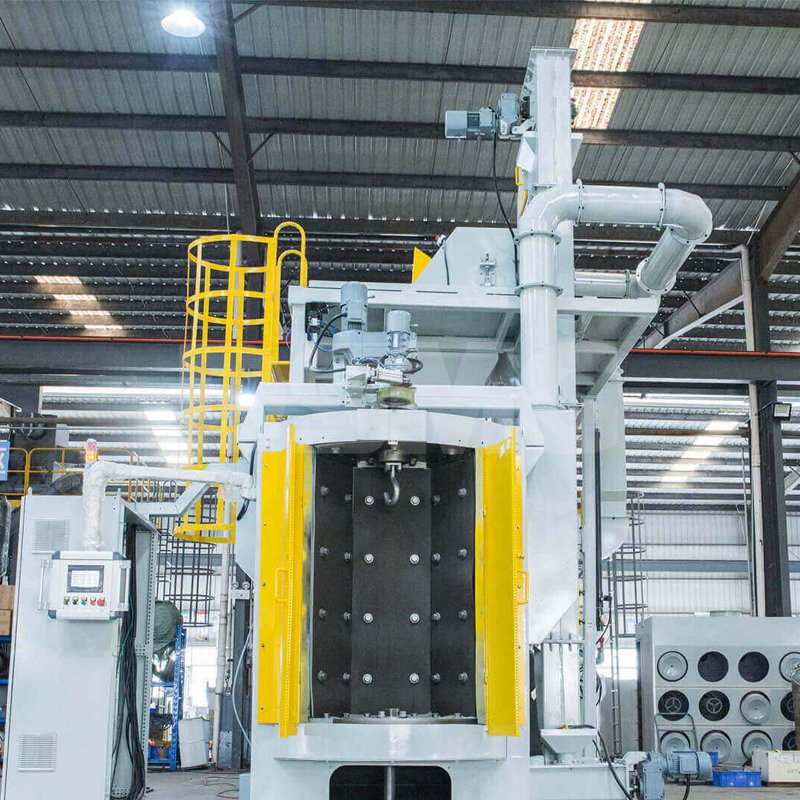
Disa has designed, manufactured, installed, and commissioned 5 SPH Spinner-Hanger type machine internal shot blasting process for Xinan casting Co., Ltd., specifically for surface pretreatment of aluminum die-cast automotive engine components.
Structure & Operation:
Shot Blasting Chamber with Wear-Resistant Liners
The double-station rotary hook-type shot blasting machine features a blasting chamber lined with abrasion-resistant wear plates.
The blasting chamber rotates at 2.5 RPM (low speed, high torque) driven by an electric motor and gear reducer.
The stopping position of the blasting chamber is adjustable via interconnected limit switches at the top of the chamber. The number of stopping positions can be customized by the customer.
Rotating Hooks & Shot Projection
Each blasting chamber is equipped with one rotating hook, which can load castings and maintain continuous rotation during blasting.
At each stopping position, abrasive media enters two direct-connected blast wheels (operating at ~3,000 RPM). The media is accelerated by the wheel blades and propelled at high velocity.
After blasting, media falls through specially designed discharge holes at the chamber bottom into a primary media screen.
Media Circulation & Separation
A screw conveyor transfers media from the blasting chamber to a bucket elevator, which lifts it into a media separator.
The separator uses airflow to remove contaminants from the media. Cleaned media accumulates in a storage hopper (mounted above the blasting chamber) to supply the blast wheels.
Dust and contaminants are extracted and processed by the dust collection system.
Dual-Zone Rotational Design
The blasting drum is divided into 2–3 sections. Driven by a motor and gear reducer (mounted on the chamber top), this design allows simultaneous operation:
Zone 1: Blasting in progress.
Zone 2: Loading/unloading of workpieces.
After blasting, the drum rotates to alternate zones cyclically.
Liner Maintenance Criteria
Wear plates are installed to extend the chamber wall’s service life.
Design requirements: Liner positioning and dimensions must facilitate maintenance and replacement.
Replacement thresholds:
Liners must be replaced when worn to 50% of original thickness or if severe perforations occur.
Failure to replace worn liners may cause damage to internal chamber components.