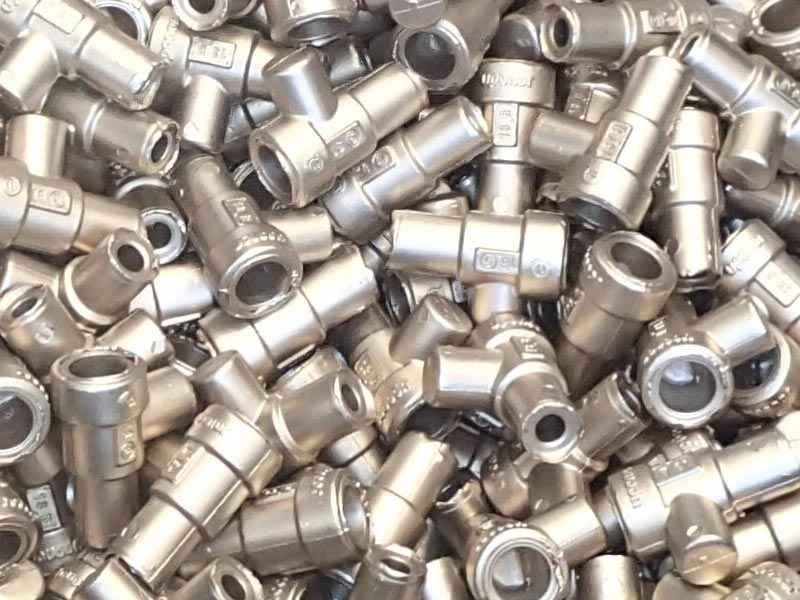
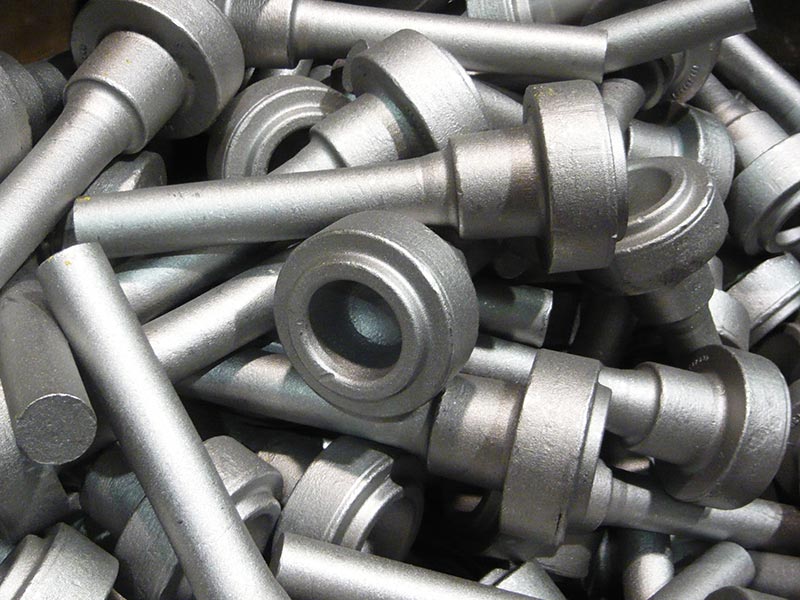
Workpieces are placed in standard turnover baskets. the feeder lift it to the door of the shot blasting machine, and the machine door immediately opens. After reaching the correct height, the workpieces are unloaded into the drum. The control process can be specified by PLC or completed manually. At this time, the drum is in the loading position. Before the blasting process, the machine door is closed, and the drum swings to the ideal position in front of the high-performance shot blaster. At the same time, it rotates around its own axis.
Open the chamber after the shot blasting process is completed, lower the drum for unloading. The workpiece blasted is transported to the material basket through the vibrating discharge chute. Here, it is further ensured that there is no abrasive on the workpiece. The used steel shots are in continuous circulation. The recovery hopper below the shot blasting chamber transports the used and dusty abrasive to the bucket conveyor. After reaching the cleaning station at the top, the abrasive is cleaned by air to remove dust and particles that are too small in size. These exhaust gas are also transported to the cartridge dust collector.
After the shot blasting process is completed, there will be a cleaning stage to remove fine abrasive on the drum and workpieces. Dust is separated by compressed air and collected in the collection tank installed below, which can be easily emptied.
The main lining of the hot area of the shot blasting machine is composed of high-strength, replaceable steel plates. During the blasting process, the door remains closed and can only be opened again after the blasting chamber is dust-free. During the blasting process, a slight vacuum is used to suck out the dust generated during the blasting process and separate it in the relevant filtration system.
This device is very suitable for processing bulk materials and has many important advantages:
Since the drum is in one piece, clamping of workpieces is avoided. In addition, the drum can be easily completely emptied, thus avoiding double processing of each workpiece.
The drum is made of perforated high manganese steel and has high wear resistance. The size of the holes depends on the size of the workpiece as well as the amount of abrasive . Complex equipment supports the mixing of workpieces.