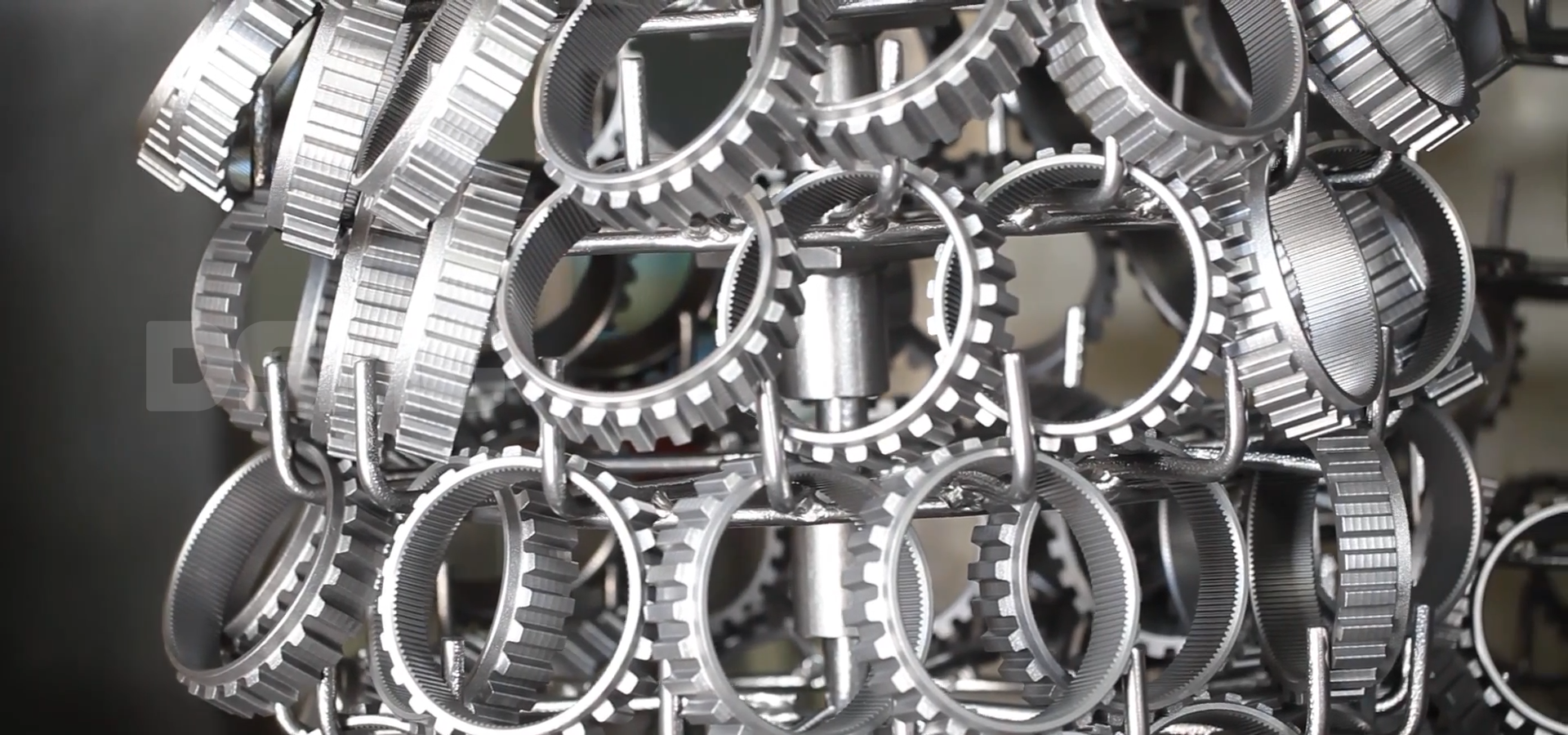
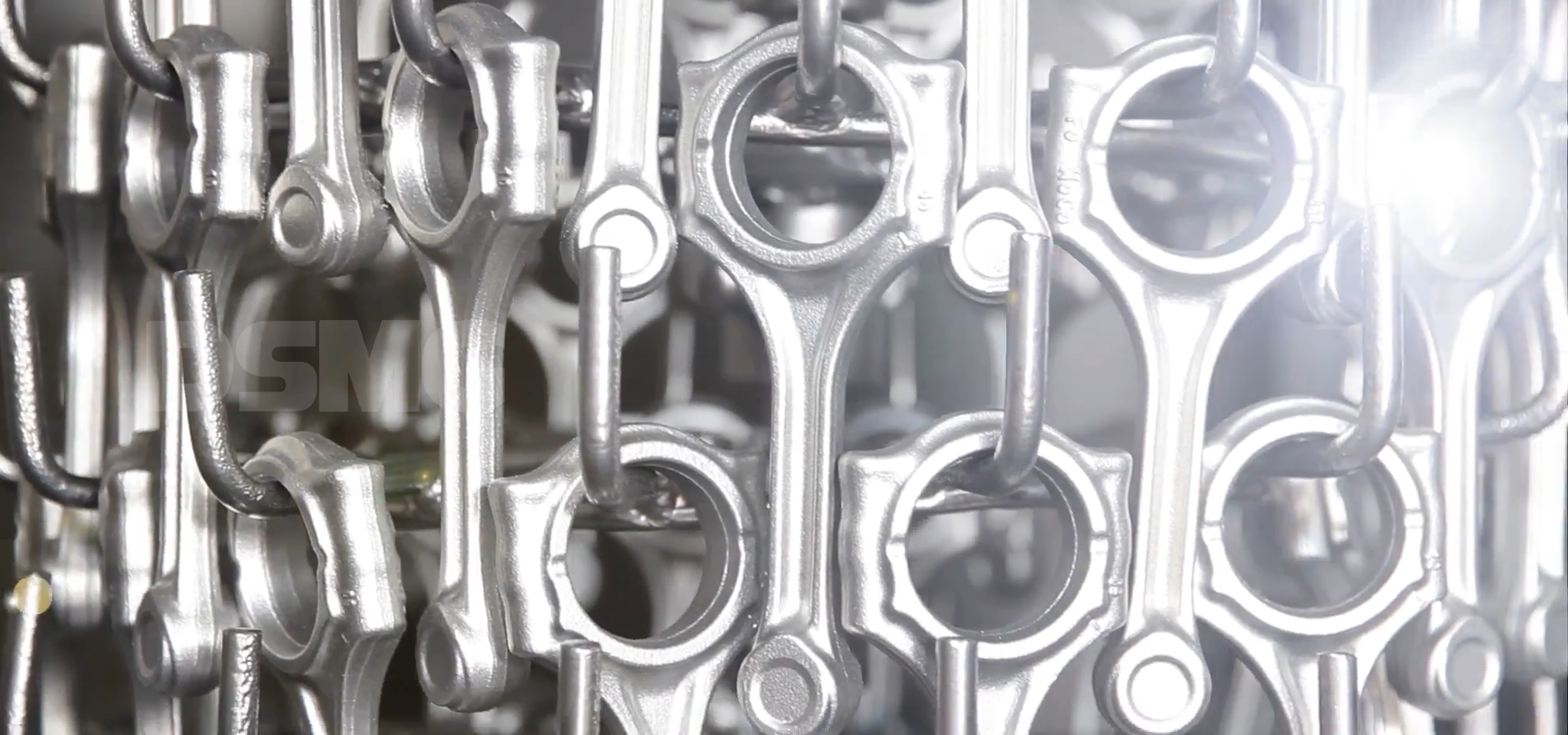
The hook type shot blasting machine is applicable for the surface cleaning of many kinds of workpieces in different manufacturing fields, and meanwhile can solve the problem of conveying various specifications of workpieces. We provide a complete solution for efficient and economic blasting and strengthening of the surface of the workpiece. Unique design of the blast wheel position can ensure that the surface of the workpiece, even the dented surface can be blasted completely.
The blasting machine is equipped with abrasive blasting turbines .This is usually offered as a inline solution for foundries, paint shops and surface treatment lines. These machines often have semi-automatic mechanism or can also be made with fully automatic blasting capabilities.
Wheel blasting cabin
The blasting cabin of the spinner hanger blasting machine is the space where the main blasting action occurs. The media is ejected out of the blasting wheels and impacts the products to be blasted. The cabin is built sturdily to ensure long life.
On the inner surface of the blast chamber, special high-wear-resistant manganese steel plates are used as linings.
Automated doors with dust seals
The doors are automatically actuated to reduce the manual effort by the operators and also ensure good sealing against dust leakages. The top of the doors are provided with openings to enable transport of the products into and out of the blasting cabin. These openings have specially designed rubber flaps and sluices to ensure blockage against dust leakage.
Safety barrier and service platform
The spinner hanger blast machine can be provided with a safety barrier in front of the machine for added personal safety. Special sensors are placed on the barrier and if a person enters the zone between the machine and the barrier, the system stops by safety override.
Screw conveyor and elevator
The shot blasting equipment has a system which enables the continuous recovery and the reconditioning of the grit or abrasive media from the system to reuse the blast media. Once the grit or the blast media has impacted the part surface and thus dissipated most of its kinetic energy while accomplishing the abrasive action, it is collected from the bottom of the hopper-shaped chamber and then transported via a scroll conveyor to the bucket elevator.
This elevator lifts the grit up to the cleaning unit. It consists of a vertical housing with a pulley in the elevator head and a pulley in the elevator base. An endless belt on which steel cups are mounted runs over these pulleys. These cups scoop the abrasive media in the elevator foot, transport it to the elevator head and dump the abrasive media in the outlet towards the media cleaner.
Elevator head
The elevator head is provided with a geared motor which drives the elevator belt. A pulley is mounted on the output shaft. The geared motor is mounted on a flange plate which is mounted on a tensioning device.
Elevator lift
The elevator takes the abrasive from the lowest level to the highest level in the abrasive recovery system. It is simply an electrically powered belt with cups that raise up to thousands of kilos of abrasive + dust per hour to be separated. The cups each have a capacity of approximately 5 kg.
How does a hook-type shot blasting machine work?
The hook-type shot blasting machine achieves uniform cleaning and strengthening of the surface of workpieces through the following steps:
Hanging and Rotating of Workpieces
Workpieces are hung on the hook trolley either individually or in strings according to their size. Driven by a three-phase gear motor, the hook adopts a motion mode of bidirectional swinging + rotating after entering the shot blasting chamber, ensuring that all surfaces of the workpieces are evenly exposed to the shot flow. This motion mode adjusts the rotation speed of the shot blasting head (1500-3200 RPM) through the frequency converter of the electrical control cabinet to meet the processing requirements of different workpieces.
High-speed Shot Blasting
The main principle of shot blasting lies in rapidly propelling a controlled stream of abrasive shot material towards the target surface. The core component of the shot blasting system is a shot blasting impeller. The shot blasting machine uses a direct-drive impeller (φ380 mm), equipped with 8 high-chromium alloy blades (55 HRC), and is driven by a Siemens three-phase motor. After being accelerated by the shot distributing wheel and the orientation sleeve, the shots impact the surface of the workpieces at a maximum speed of 73 m/s, and the coverage intensity can be precisely controlled by adjusting the rotation speed of the shot blasting head.
Shot Recycling and Impurity Separation
The shot and debris after blasting are conveyed to the bucket elevator (manganese steel lifting bucket) through the bottom screw conveyor. Then they enter the air separation separator, where impurities such as scale and debris are removed through gravitational screening and magnetic separation, and the pure shots are stored in the hopper for future use.
Dust Treatment and Clean Air Discharge
The dust removal system adopts a two-stage filtration method:
The primary cyclone separator deals with large-particle dust;
The high-efficiency bag filter (>99% efficiency) captures micron-sized particles;
The purified air is discharged through the negative pressure system (with an air volume of 38,000 m³/h), and the noise is controlled at ≤85 dB(A) through sound insulation design.
Automated Control and Safety Mechanisms
The PLC program control adjusts the shot blasting time, the rotation speed of the shot blasting head, and the movement of the hook;
Door lock interlock: The pneumatic double-opening doors are automatically locked during shot blasting;
The emergency stop button and the vibration monitoring device prevent the equipment from overloading.