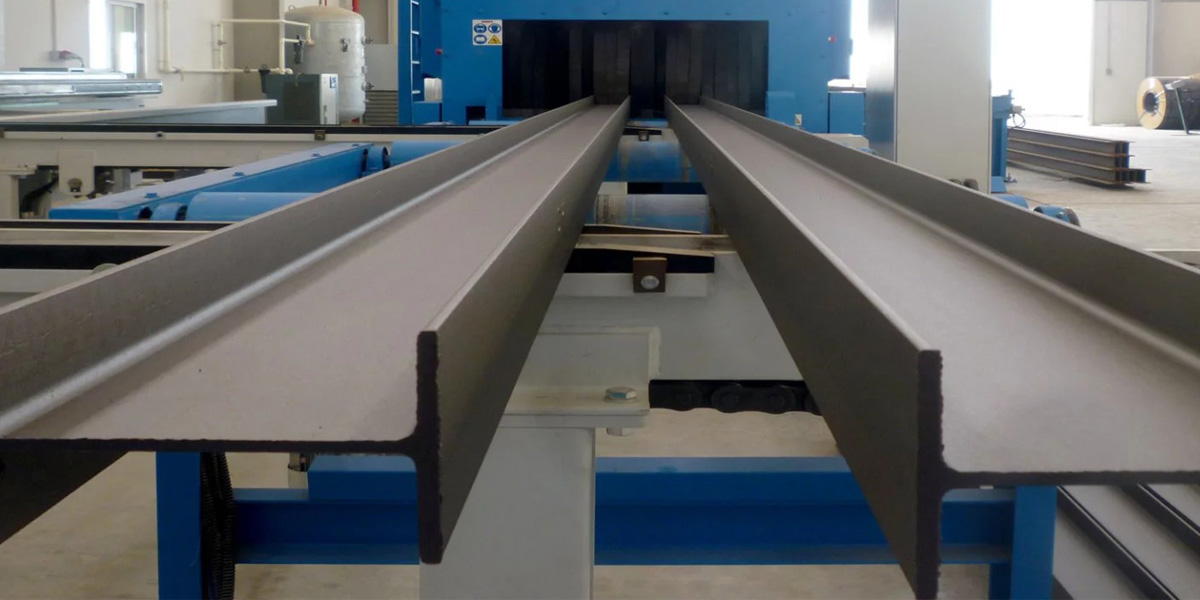
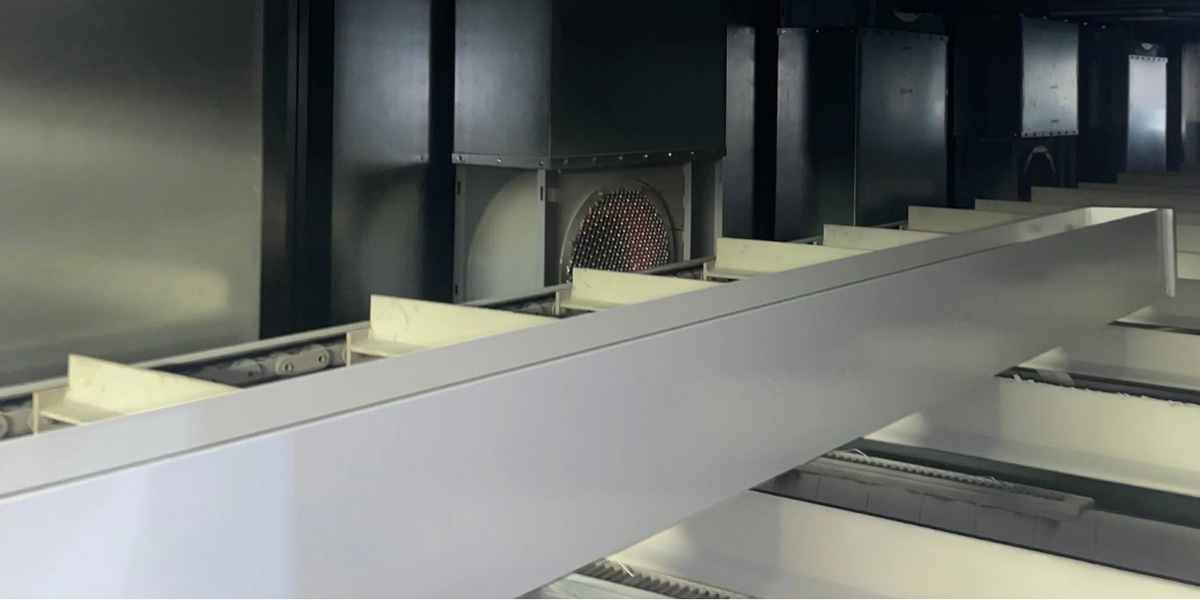
Roller conveyor shot blasting machine is designed and manufactured to clean the surface of the large, long and /or flat components such as section steel etc. It is mainly used for removing the rust, scale ,paint and contamination from the steel surface such as large scale H-Beam and I-Beam in the construction and bridge.A complete system include:
1.Roller conveyors,
2.Shot Blasting Chamber,
3.Abrasives recovery & Separate System,
4.Abrasives blower off system,
5.Dust collector and Control Panel
Our advantage:
Improved air separator for removing undersided particles and for cleaning of abrasive.
Durable machine housing made from extra hard manganese steel
A large maintenance plateform for hassle free access to the wind separator and bucket elevator portions of the machine
Machine concept—easy to maintain
Exchange of filter cartridges is easy,quick and easy
Easily exchanged manganese steel plates in the direct blasting path of the turbines
Easily exchange wear resistant rubber curtains for containing particulate within the operating area of the machine
Technical Description
Disa roller conveyor shot blasting machines are specially designed for shot blasting of plates and profiles and are made out of high quality components, giving the best blasting results. Long lifetime components are used to minimize the wearof the machine, which is essential on the inside due to the blasting process. Pre-installed blasting programs and automatic functions make the shot blasters fast and easy to work with. The compact design of the shot blaster reduces the required working space to a minimum, without compromising on functionality and quality.
Advantage:
Can operate on a continuous, unmanned operation with the effectiveness of batch cleaning.
Fully automated system designed to descale and remove rust from plate and structural members prior to fabrication.
Specially developed to meet the needs of the fabrication industry.
Effectively cleans large workpieces, eliminating the environmental problems and high labor costs associated with manual air blasting.
1.Heavy-duty blasting wheels
The Blasting Wheel is precision balanced and hardened for 55 HRC by Special Hardening Process. Hard Blasting Blades (8 Nos.) are provided with Hi Moly., Hi Chrome composition giving longer life. The Control Cage Impellers are also made of Hi Moly, Hi Chrome. All Liners are Hi Manganese Quality for longer life.
Each turbine set has a separate abrasive valve to start the abrasive flow only when material reaches the turbine, so damage to the machine because of running empty is minimized.
All motors are totally enclosed fan cooled to provide maximum life.
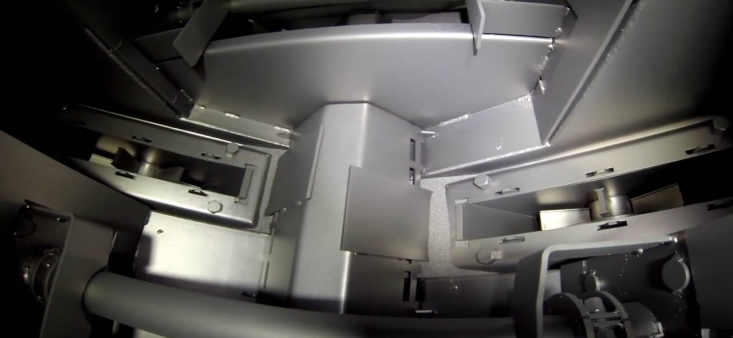
2.Machine housing
a. Made of 12mm steel plates welded with section bars are used for the chamber body, so they are solid and reliable., with abrasive collection hopper as well as grid, to accommodate the three blast wheels. The slot in the roof for putting through the hooks is sealed by rubber and brushes
b. Double wing doors, pnematic-mechanical actuated, material no. St 37, lined with hard easy-changed manganese steel plate, controlled by the automatic machine cycle. In the machine housing, i.e. in the so called "Hot-Area": replaceable plates of hard manganese steel 13 % MN, mat.-no. Mn13. The plates are 15 mm thick. They are held in position by hardened cap nuts and/or hanged in.
c. 6mm steel plates welded with section bars are used for the door body. A labyrinth sealing structure is adopted between the door body and the room body.
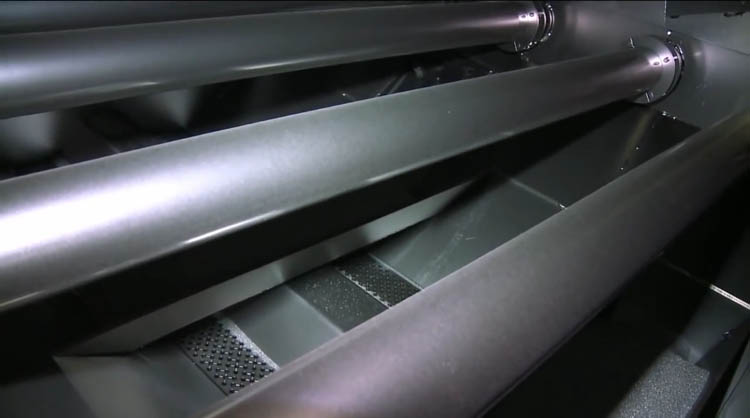
3.Hardened rolls
The rolls inside the blasting cabinet are from thick hardened steel to make sure they do not wear during the blasting process.
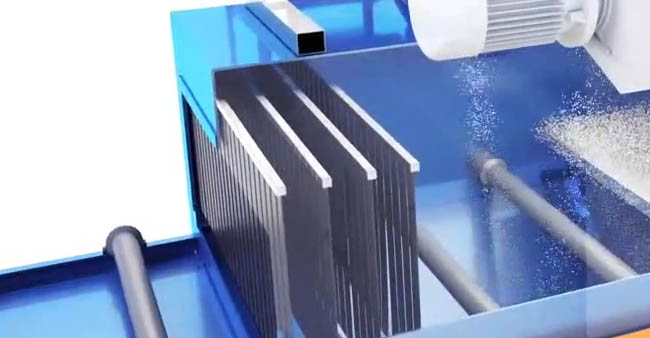
4.Auxiliary chamber
There are 5 layers of wear-resisting rubber curtain in it. The suspension type makes the exchange and access easier.
The seal ability is excellent. No dust would be leaked out because of the negative pressure formed by the dust collector fan.
lid of the blast wheel is fitted with a safety switch.
5.Light curtains
A light curtain detects the front and back side of the product. Therefor the machine opens the valve for the abrasive, only then when there is material. This increases the life time of the wear plates.
6.Abrasive Circulation System
From the elevator the abrasive is deposited into the air wash screw conveyor.
The screw conveyor takes the abrasive to the air wash unit where a uniform curtain of abrasive is made by an adjustable stratification plate.
The abrasive flows down the stratification plate and over the air wash zone where suction from the dust collector removes the fines and other contaminants.
The abrasive then passes through a mesh sieve where any oversize particles are retained so that they cannot get into the abrasive hopper.
The abrasive then falls into the storage hopper ready for use.
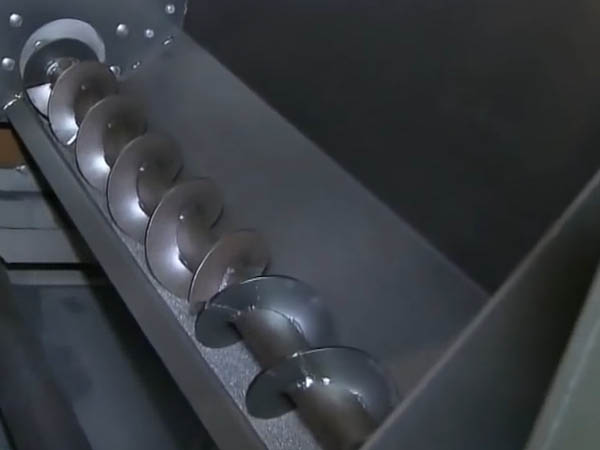
6.1. Bottom spiral
6 mm high-quality carbon steel welding is adopted for the shell;
16Mn material is adopted for the blades and wear-resistant material is welded on the top of the blades;
Labyrinth seal is adopted in order to prevent abrasives from overflow;
Stopping detection device is arranged
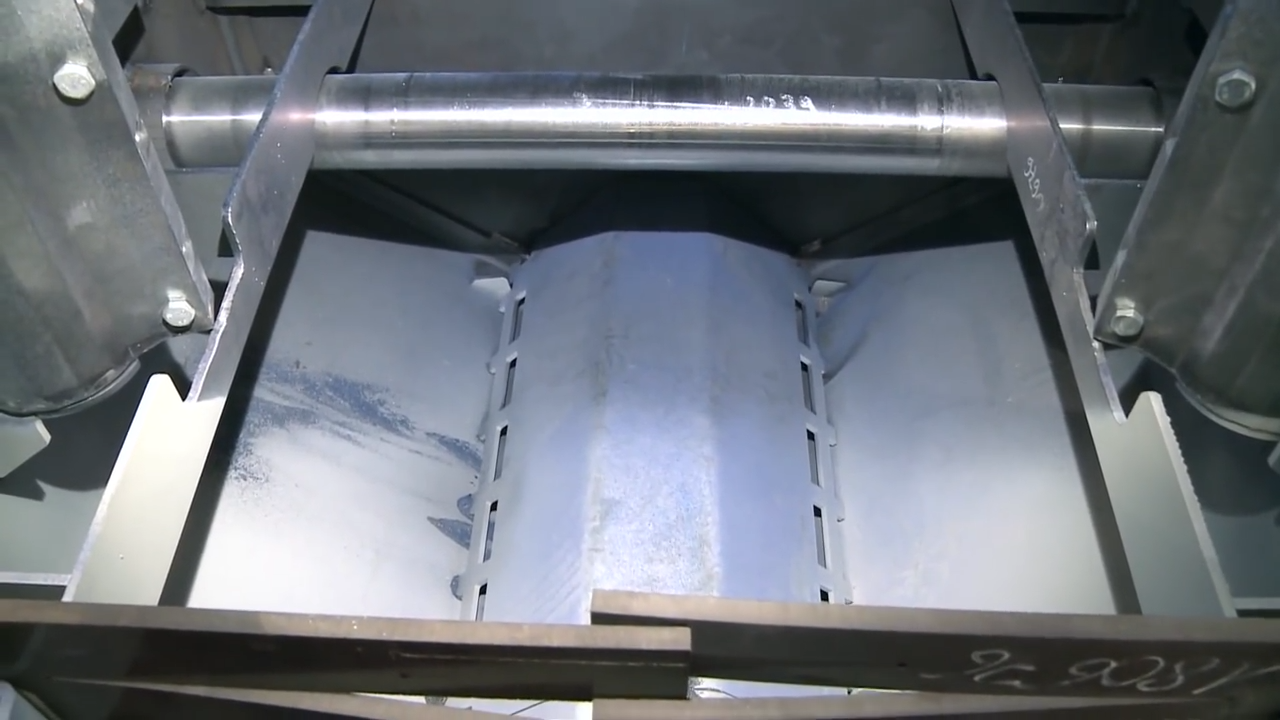
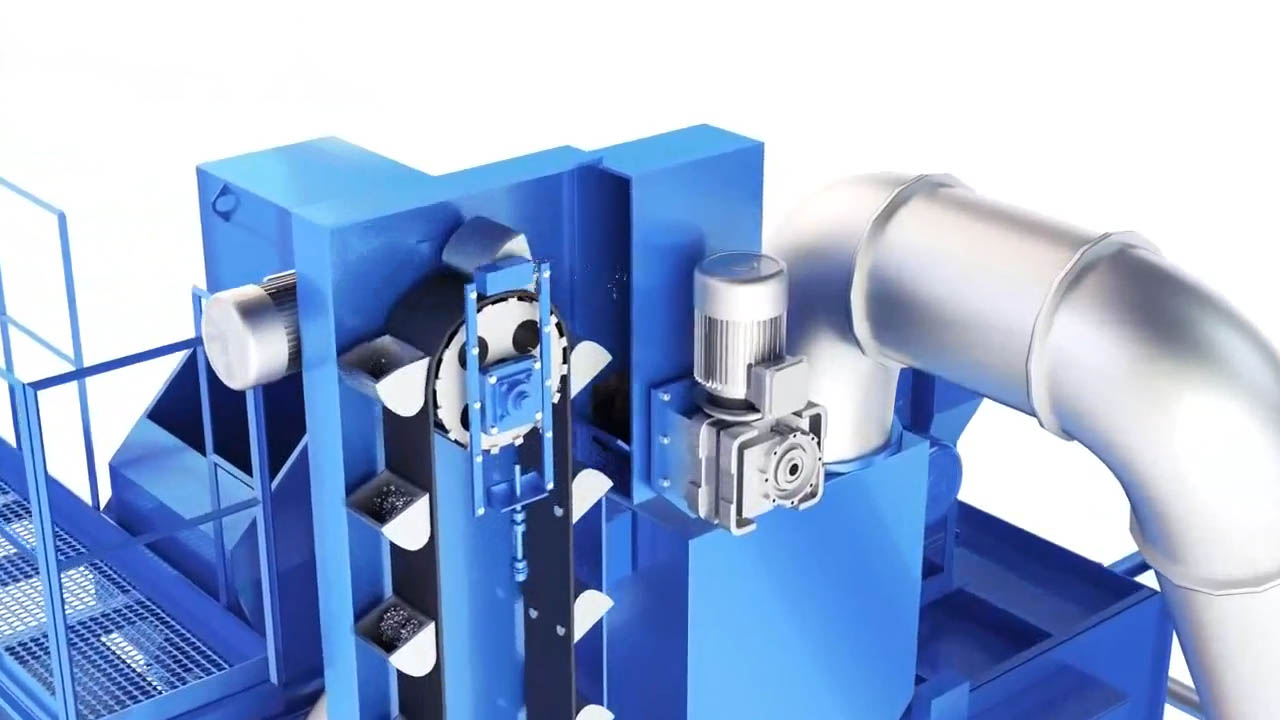
6.2. Bucket elevator
4-6mm high-quality carbon steel welding is adopted for the shell;
Anti-reverse mechanism is adopted on the top;
Stopping detection device is arranged at the bottom
Special elevator belt is adopted.
To take the abrasive from the shot blast cabin to the bucket elevator, with separation of coarse particulates, and to discharge the cleaned castings.
4-6mm high-quality carbon steel welding is adopted for the shell;
Anti-reverse mechanism is adopted on the top;
Stopping detection device is arranged at the bottom
Special elevator belt is adopted.
Pulse wheels are installed on the lower shaft of the elevator and the working condition of the elevator can be detected. The signals can be timely fed back to PLC for processing, so that safe operation of the machine is assured.
6.3. Top spiral
6mm high-quality carbon steel welding is adopted for the shell;
Abrasive adjusting valve is arranged and uniform abrasive arrangement can be realized; stopping detection device and overflow device are arranged; A labyrinth structure is set to prevent abrasive from overflow.
Cascade-type air wash separator To separate impurities from the circulating abrasive, equipped with expansion box for the separation of heavy contaminants, abrasive storage bin, distributor valve and dust downpipe.
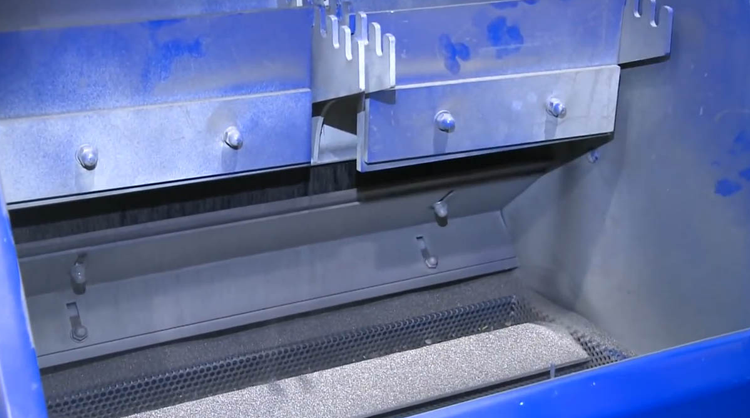
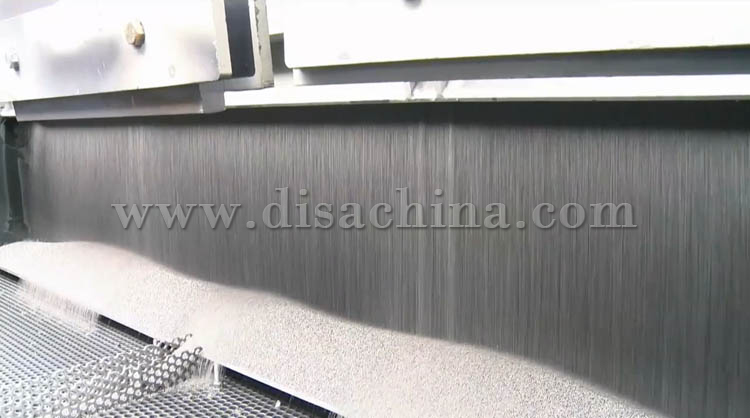
6.4. Cascade-type air wash separator
To separate impurities from the circulating abrasive, equipped with expansion box for the separation of heavy contaminants, abrasive storage bin, distributor valve and dust downpipe.
An adjusting gate, which can assure uniform abrasive arrangement, is arranged. An adjusting plate is arranged at the exhaust inlet.
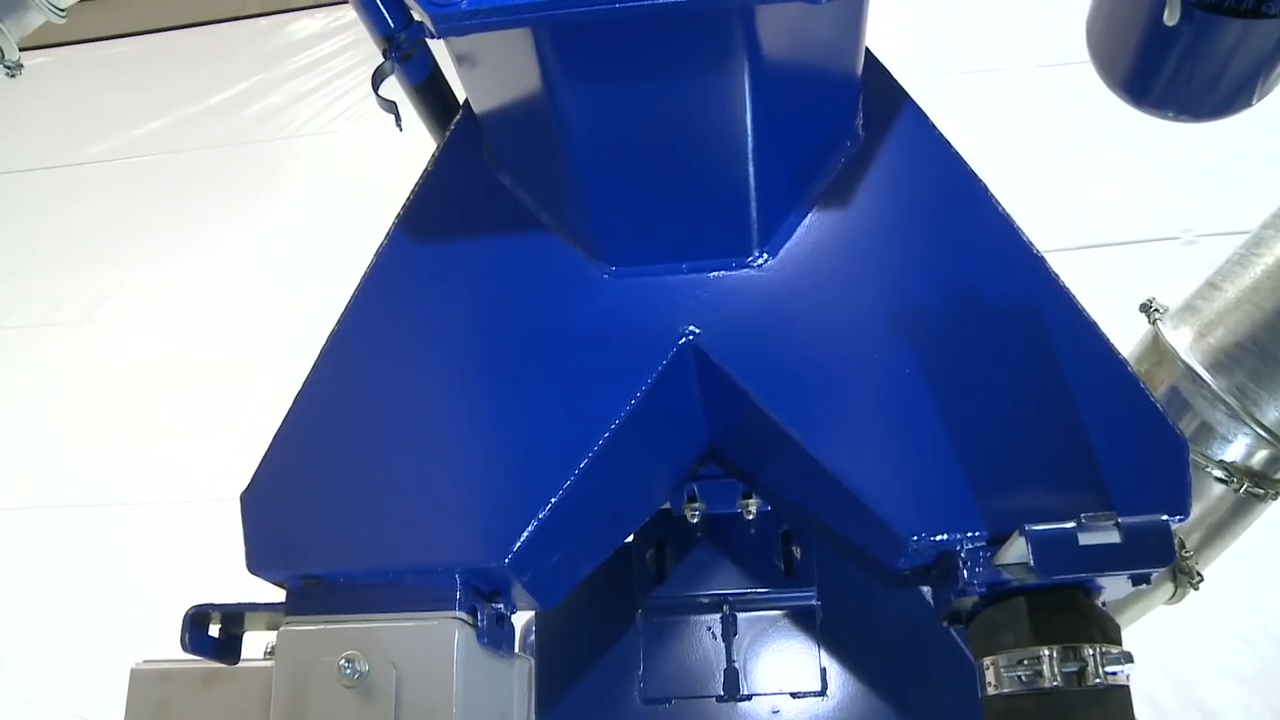
6.5. Storage hopper
Storage hopper of shot blasting machine is situated under a separator and holds enough abrasive to supply the blast wheels for uninterrupted blasting through the process.
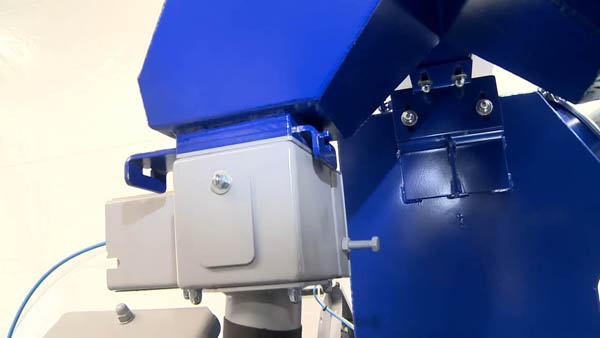
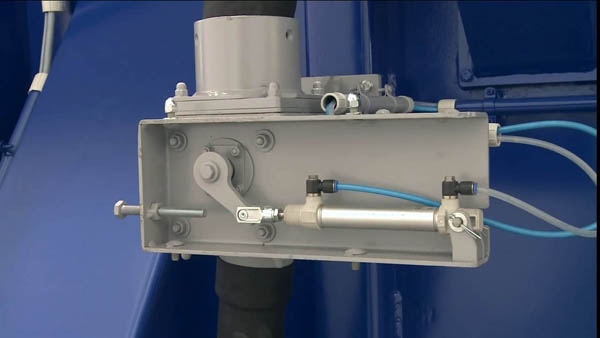
6.6. Abrasive control valve
Feed pipes are hoses connecting the storage hopper and blast wheels. Slide gates located under storage hopper can be closed to allow for maintenance. In line with feed pipes are abrasive control valves, located just above the blast wheel DISA abrasive control valves; totally enclosed for noise reduction - pneumatic operation with fine adjustment capability to control the flow and volume of abrasive supplied.
Pneumatic control;
Abrasive adjusting device is arranged;
The sturcture is simple and reliable;
Air cylinder control stroke is adopted and the blasting capacity is remotely controlled, so that the abrasive control valve can be closed.
6.7 cyclone settling chamber
The abrasive material thrown by the blast wheel passes through small orifices located at the lower part of the revolving drum and is conveyed to the base of the bucket elevator, which conveys the abrasive material still contaminated by impurities to the abrasive purifier, which will operate through the air washing system. To complement this system, the equipment features a cyclone that prevents the loss of abrasive material to the exhaust system.
7. Dust Collector
The dust laden air enters the dust collector through side and passes into a settling and equalizing compartment. Through expansion in the equalizing compartment, the air velocity drops and flow is distributed over the entire settling area. The air then flows up and away from storage hopper causing the heavier dust particles to settle down, the fine particles floating upward into filter tube. The clean air passes through the tubes and is exhausted through the blower. At certain interval the tubes are shaken mechanically/manually to remove the accumulated dust from the filter bags. The dust is collected in the tray of the dust collector. The trays are taken out periodically and emptied. The filter bags are made out of a satin weave filter cloth. The seams are multiple stitched with heavy cotton thread.
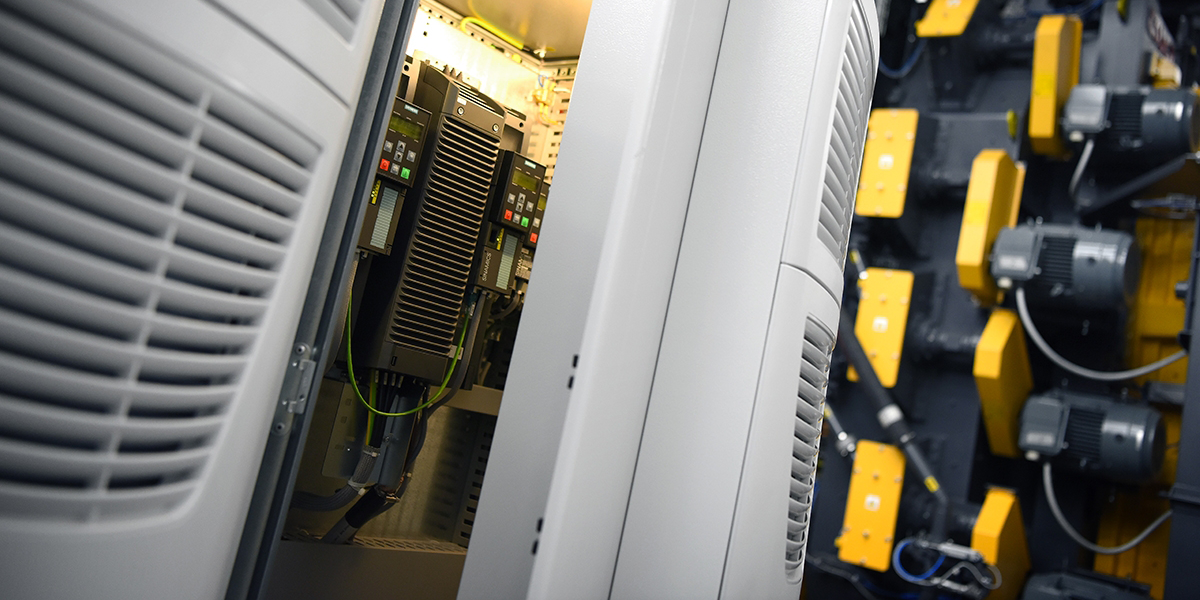
8.Electric control system
The electrical control system for three-phase AC frequency 50 HZ voltage 380 V power distribution.
The shot blasting machine electrical system has the following features:
The blasting wheel, maintenance door, abrasive controller and abrasive circulation system are equipped with electric
interlock and self-locking system to ensure the reliable operation of the equipment and the safety of operators.
This system's blast wheel running conditions adopts the ammeter monitoring control, on the one hand, can through
the ammeter to protect blast wheel, on the other hand can monitor the blast of the empty cast, the phenomenon
such as jam, in order to adjust the equipment working state.