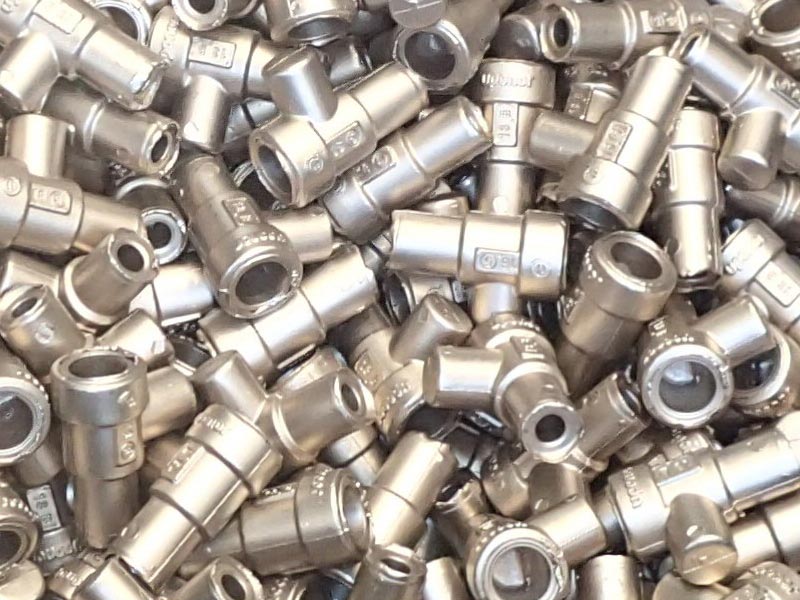
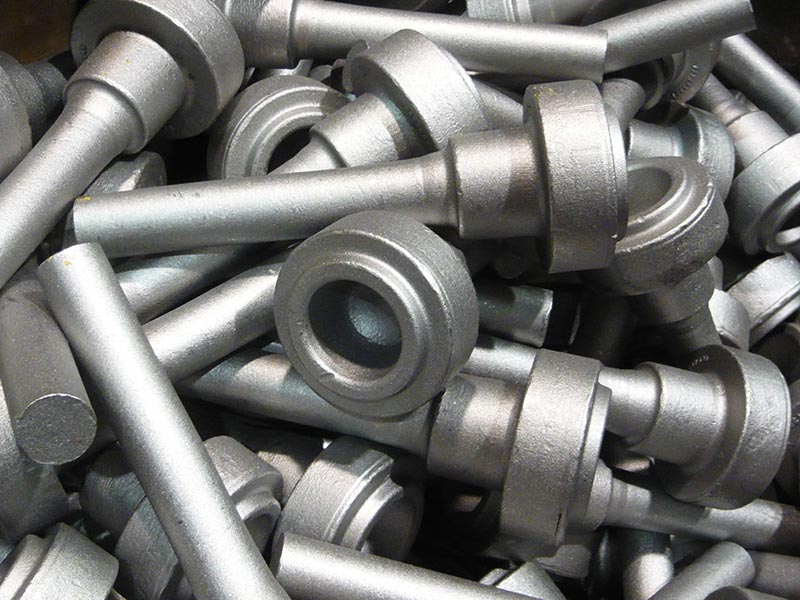
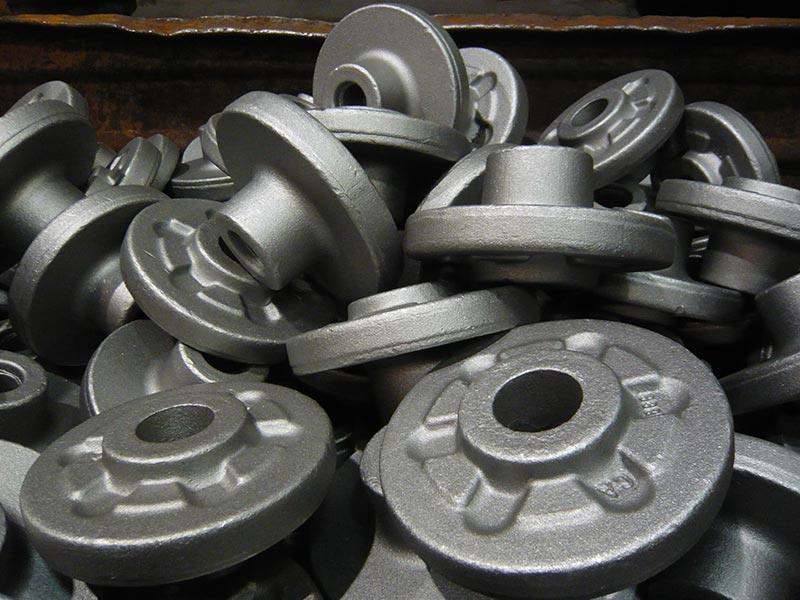
Working principal: when a specified amount of workpieces are added in the blasting chamber and the machine is started, the shots which are blasted by the blast wheels form projectile beam and are evenly attacked on the surfaces of the workpieces to achieve the purpose of cleaning and strengthening. The blasted abrasives and grits flow into the elevator and elevated to the separator through the elevator for separation. The dust is pumped into the dust collector through the fan for filtering and the clean air is discharged into atmosphere. The dust in the bags is mechanically shaken and fallen into the dust collecting box at the bottom of the dust collector. Users can regularly remove the waste grits and the waste grits are discharged from the waste grit pipes and can be recycled. The shot grit mixtures are collected in the chamber body through the recycling pipes. When the mixtures are separated in the separator, the clean projectiles flow into the blast wheels to blast workpieces.
Tumble rubber belt shot blasting machines are perfect for cleaning parts that can be batched and tumbled in large groups. Parts tumble in a "C" configured conveyor belt system while a blast wheel propels abrasive into the cup of the C. Ease-of-use and ease-of-maintenance are key design elements providing maximum productive work hours. Batch blasting is the most cost-effective method of blasting, provided components can tolerate the tumbling action. Batch barrels can be integrated with a variety of material handling options to provide a range of automation levels including fully automated systems.
Tumble Belt Type Shot Blaster Machine Advantage:
1. Used for surface cleaning, rust removing and surface intensification of various middle and small size casting, forging and workpieces.
2. Suitable for different production scale and can also be used in conjunction with the continuous conveyor components to form the production of clean-up lines.
3. Advanced design, reasonable structure
4. Little energy consumption and high efficiency.
5. This machine adopted the double plate impeller head, characterized as brief structure, easy to change impeller and high shot blast efficiency.
6. Efficient separator of shot from sand, high separating quality and productivity, long impeller lifetime.
A:The rubber crawler belt type shot blasting machine is extremely suitable for cleaning workpieces that can be processed in batches and undergo large-scale tumbling. In the "C"-configured conveyor belt system, the workpieces keep tumbling. At the same time, the shot blasting wheel will hurl the abrasive at high speed into the "C" groove to effectively clean the surface of the workpieces. The device attaches great importance to the convenience of operation and the simplicity of maintenance in its design. These key design elements ensure that the equipment can achieve the longest effective working hours.
Batch shot blasting is a highly cost-effective shot blasting method. However, it is necessary that the workpiece components can withstand the forces during the tumbling process. The batch drum can be combined with a variety of material handling configuration options, thus providing different levels of automated operation solutions, including even fully automated systems, to meet diverse production needs.
Q2: What is the operational principle?
A: Workpieces are loaded into the machine’s chamber. Upon startup, turbines eject abrasives to form a controlled stream that uniformly impacts surfaces. Spent media and debris fall through belt perforations into a recycling system:
Elevators transfer material to separators for reuse.
Dust is extracted by fans through filters (e.g., baghouses), with purified air released.
Waste particles are discharged via dedicated pipes; reusable media reenter the blast wheel via electromagnetic gates.
Q3: Typical applications?
A: Widely used in foundries and forging facilities for:
▸ Mass-produced components: castings, forgings.
▸ Complex-shaped or sharp-edged parts.
▸ Surface treatments: oxide/rust removal, fatigue life enhancement.
▸ Light alloy processing, core sand elimination, and post-heat-treatment cleaning.
Q4: How does the belt structure ensure durability?
A: Key design features:
Manganese steel plates & chain links: Bolt-connected for impact resistance.
Unidirectional belt rotation: Prevents workpiece stacking.
Modular components: Allow localized replacement of worn sections.