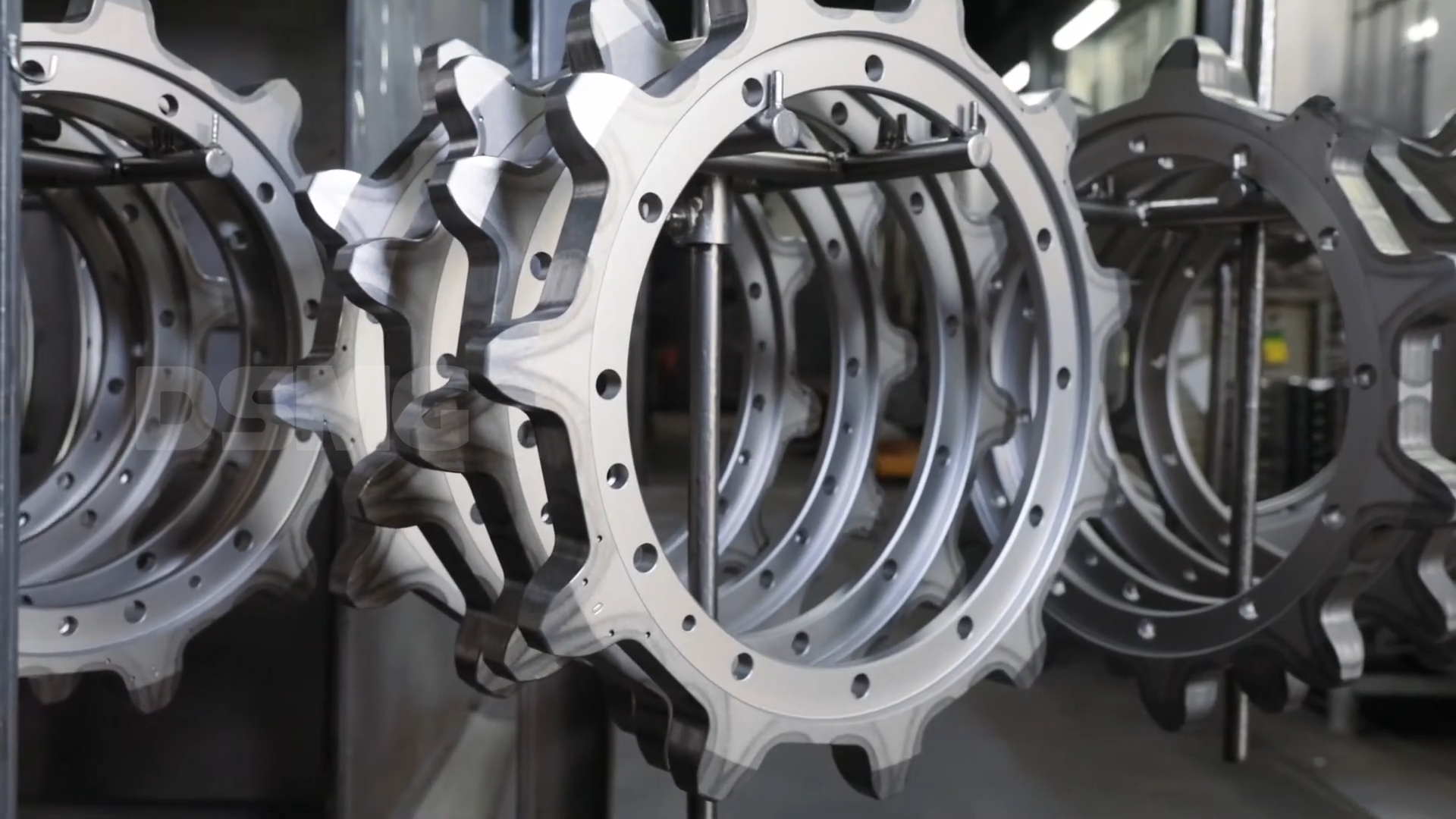
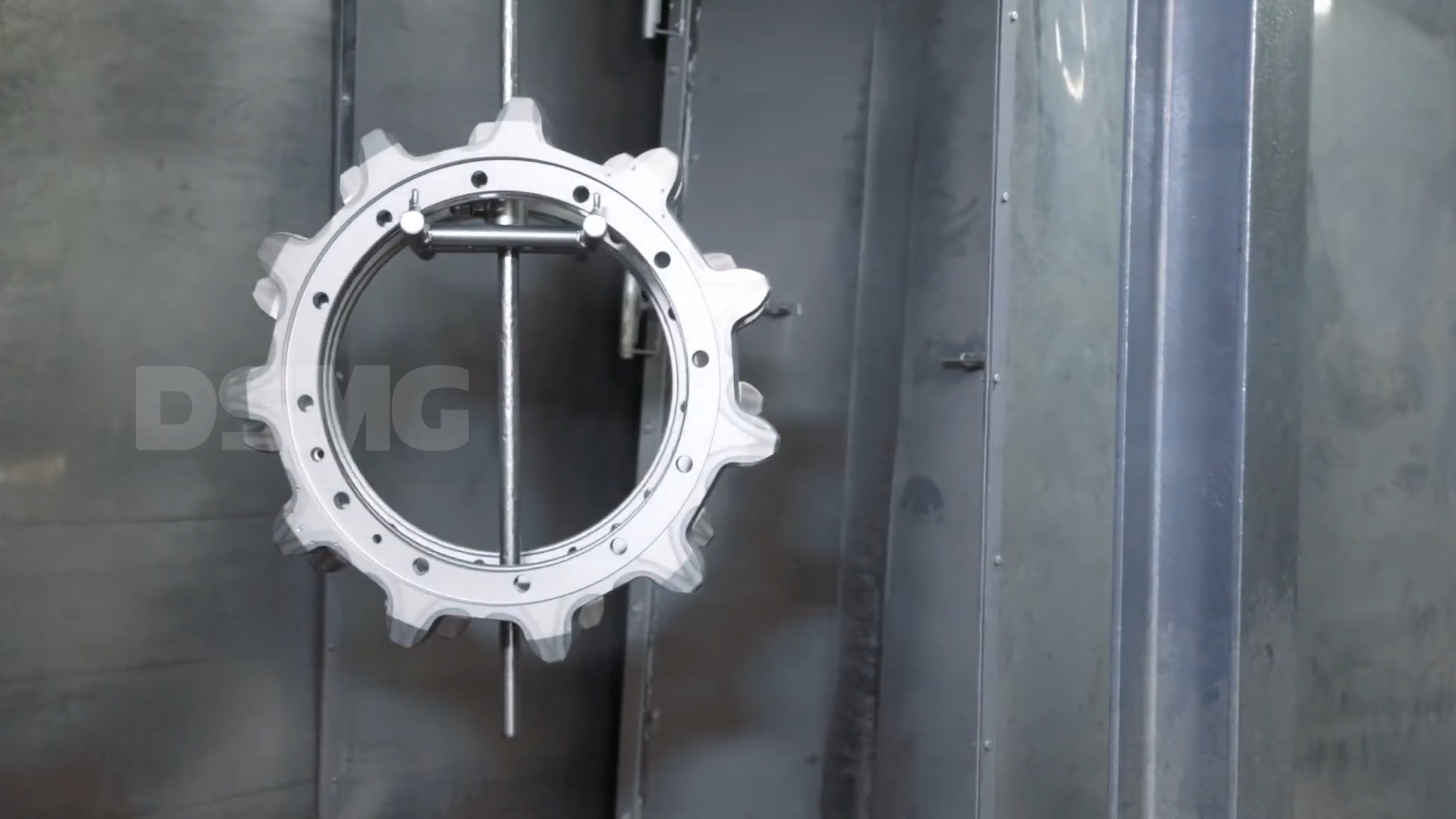
The workpieces are hung on a blasting frame or directly on the rotating hooks of the chassis and pushed up to just in front of the steel system. An automatic feed device transports them to the first beam position.
After the program has started, the machine door is automatically closed and locked . The workpieces are blasted rotating in two or three positions according to the preset blasting time.
The abrasive is kept in circulation and cleaned for continuous use.
The cleaned blasting agent is transported from the blasting agent bunker to the high-performance turbines via the blasting agent dosing device.
After the end of the blasting cycle and after the turbines have come to a standstill, the machine door opens automatically and the workpiece hanger returns to the starting position.
A fan generates the required negative pressure for dust-free operation of the blasting systems. The extracted air is cleaned with a filter system.
The main components of the shot blast machine are as follows:
Abrasive material purifier: The purifier features the traditional system with adjustable curtain, which can optionally have a screening system (vibrating screens), for applications that require a more precise classification of the abrasive material, for example, with shot peening.
Blast Wheels: Of very high output, built in cast steel with a high chrome alloy that is highly resistant to abrasion, they are statically and dynamically balanced and ensure high productivity in the most different applications. The blast wheels feature a valve that allows precision adjustment of the amount of abrasive material to be thrown by them.
Screw conveyor /bucket elevator: The conveyor and the elevator are oversized, and are totally sealed, and are driven by gear motors. The elevator buckets are built in cast nodular iron, which is highly resistant to abrasion.
Movement of hangers: The movement is executed through a gear motor that actuates a transmission chain with acts directly on the hook, where the parts to be blasted are positioned. The spinning movement produced on the hook exposes the parts to the abrasive material fan, formed by the blast wheels. This spinning movement transforms automatically into a linear movement at the moment of loading/unloading the equipment. The spinning and advancement speed of the hanger are controlled through a frequency inverter.
Exhaust system: Extremely compact, the exhaust system features cartridge-type filtering elements, with an automatic cleaning system through pulse jet, which is automatically controlled by the PLC do control panel. This system meets the most important international standards on pollutant emissions and work safety.
Optional: The machines can receive a series of optional equipment, among which, the following stand out: coatings to operate with angular abrasive materials, vibrating screen, frequency inverter for the blast wheels, etc.